Author: Carlo Carniani – Senior Petroleum Engineer
– – –
Energy transition relies on the possibility of producing renewable energy without impact on the environment, namely with no greenhouse gases production. Hydrogen represents a great opportunity to achieve this goal, since it does not release CO2 upon burning. Depending on the way hydrogen is obtained, it can be classified according to a kind of not-standard colour code. For example, grey hydrogen is the one obtained from natural gas by reforming, without capture of CO2, which is a by-product of the reforming production process.
The so called “green hydrogen” is instead a fuel obtained from renewable electricity that does not release greenhouse gases neither when it is produced nor it is when burned.
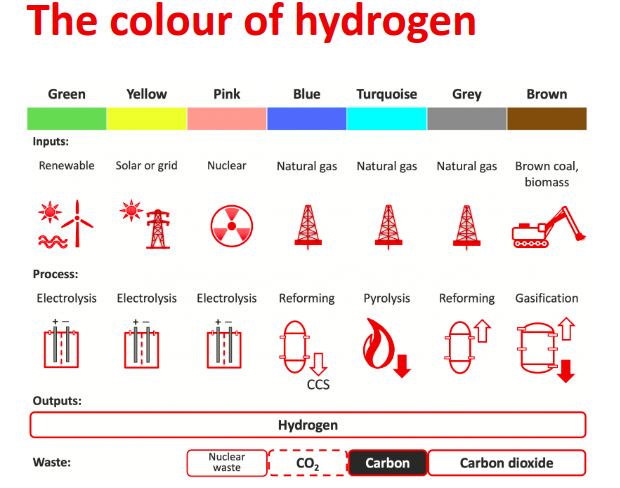
It can therefore allow the decarbonisation of transport and heavy industries that cannot be powered with traditional electric batteries, but transportation to the places of consumption is challenging: for example, hydrogen would have to be cooled to a temperature of -253°C to be liquefied, that is an exceedingly low temperature! However, if hydrogen is converted into ammonia NH3, composed of nitrogen and hydrogen, it is possible to transport it as a liquid, in a much more manageable way than high pressure gas, since ammonia liquefies at the relatively high temperature of -33.3°C,
AMMONIA (NH3) is a basic and widespread chemical present in many industrial applications, ranging from agrochemical (fertilizer production represents roughly 85% of present ammonia consumption) to military. It is presently being considered in the energy transition context as hydrogen carrier: in fact, each of its nitrogen atoms bonds to three hydrogen atoms, so that ammonia is a high hydrogen content chemical. Moreover, ammonia can be easily liquefied at atmospheric pressure, which makes it a better carrier than hydrogen gas itself. For example, a cubic meter of liquid ammonia contains about 136 Kg of H: for comparison, a cubic meter of hydrogen stored at 350 bar (a typical pressure of an automotive hydrogen tank) weighs approximately 141 Kg. A cubic meter of liquid hydrogen at -253°C, instead, weighs 71 kg.
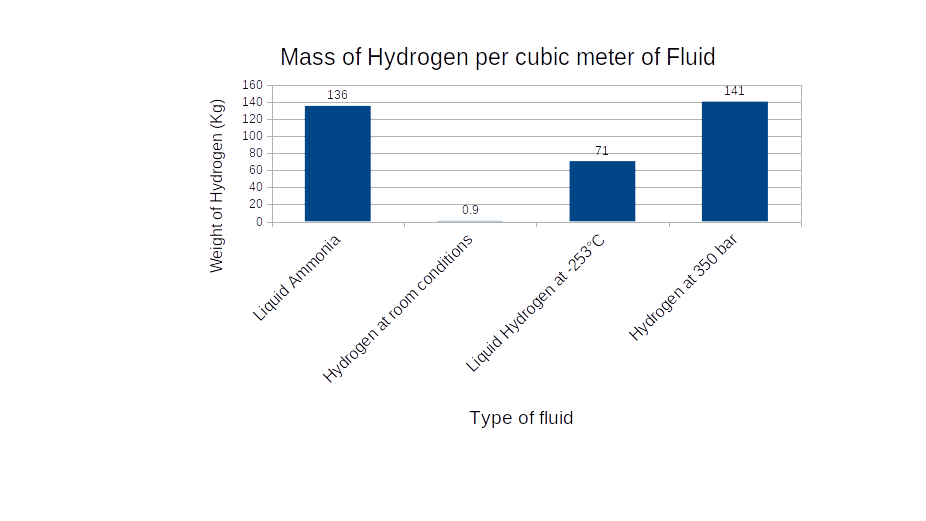
Obviously, in order to use the hydrogen contained in ammonia, the molecule must be split in order to free the three hydrogen atoms bonded to nitrogen. The industry already performs this task by using thermal processes (also known as Ammonia Cracking) that operate at 1,000°C in large plants, with catalysts made of expensive Ruthenium. The process is energy demanding and therefore produces large quantities of greenhouse gases, unless abundant renewable sources of energy (e.g., hydroelectric) are locally available.
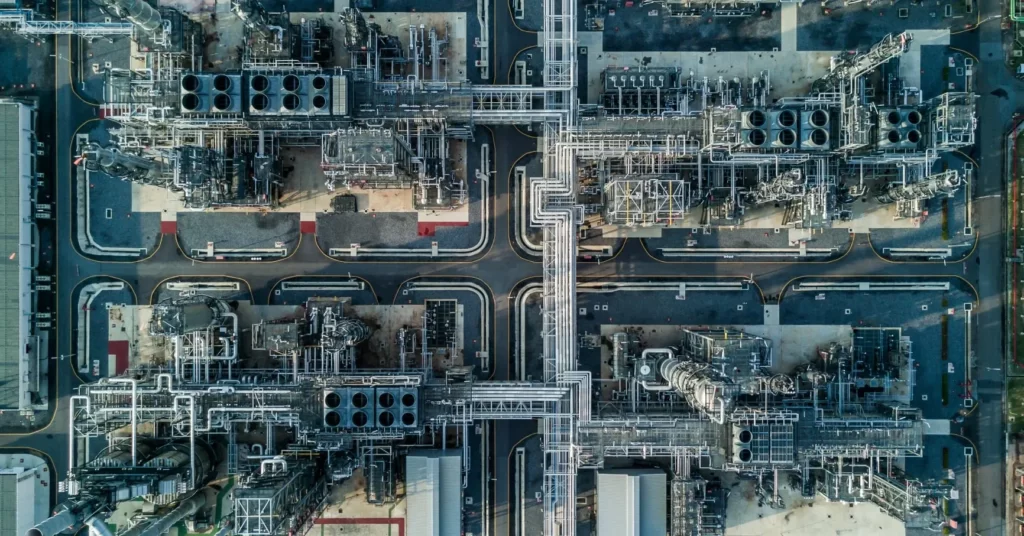
On the other hand, small to medium scale hydrogen generation plants are desirable to achieve a widespread access to hydrogen fuel usage.
Several attempts are ongoing to build more manageable ammonia cracking systems, like the somewhat bulky prototype shown in the figure below. Such a device is expected to deliver 400 kg/day of hydrogen gas.
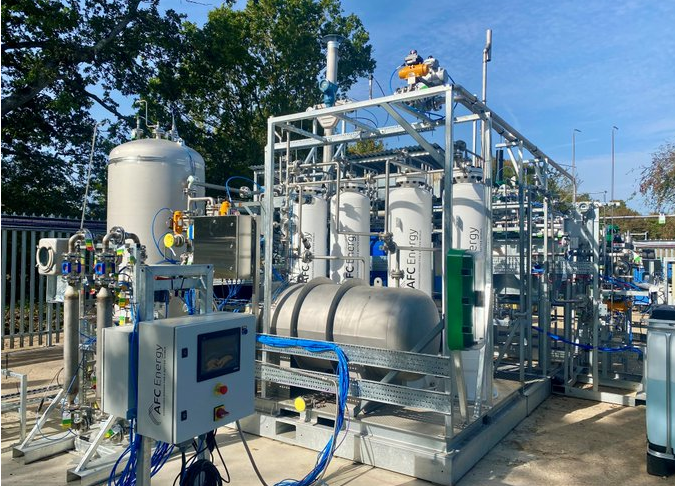
Research in progress at Rice University in Houston lead to the creation of a small device that uses LED light to convert ammonia into hydrogen, without requiring high temperatures and pressures.
It is in fact a light-driven catalyst that has, at ambient conditions, the same efficiency as thermal catalysts operating at high temperatures and pressures. Furthermore, instead of being composed of platinum group metals, such as the very expensive Ruthenium, the photocatalyst is made of cheap and abundant elements such as Copper and Iron.
Halas’ Research Group of Rice University has been working on Plasmonic application to photocatalysis for more than 30 years. Such catalysts make use of nano-particles oriented in such a way as to become antennas capable of increasing the system’s ability to absorb light. In addition, suitable metals (reactors) are incorporated into the nanoparticle surface to catalyse the actual desired chemical reaction; this is called an antenna-reactor system.
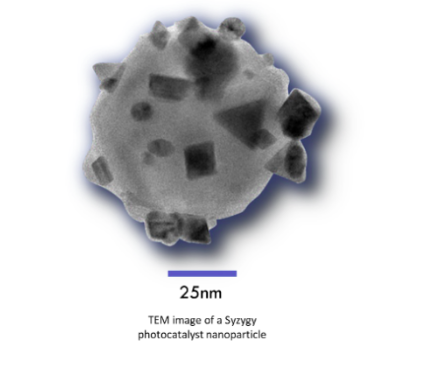
Several reactions are possible; one of the most interesting ones for energy application is the decomposition of ammonia to give hydrogen gas, emulating the thermal ammonia cracking. So far, photocatlytic ammonia decomposition has been performed using nanoparticles made of Copper and Ruthenium, a rare and expensive metallic element, needed to withstand the high temperature at which the standard reaction occurs.
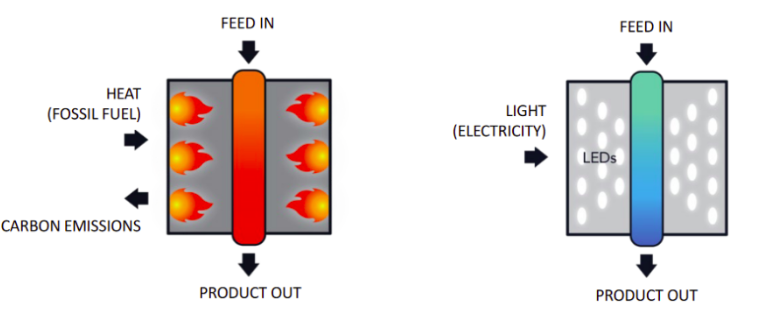
In the experiments performed at Rice University, nanoparticles are illuminated by LED light (Light Emission Diods); the antenna-reactor system absorbs light and produces “hot electrons”, i.e. short-lived electrons possessing a very high level of kinetic energy, which start an efficient chemical reaction even at room temperature.
Halas and her team succeeded in creating these photo-catalysts to split ammonia using copper for the light-collecting antenna, but replacing Ruthenium with the much less expensive Iron as reactor. Laboratory tests show that Copper-Iron catalyst has similar reactivity and comparable efficiency with respect to Copper-Ruthenium systems.
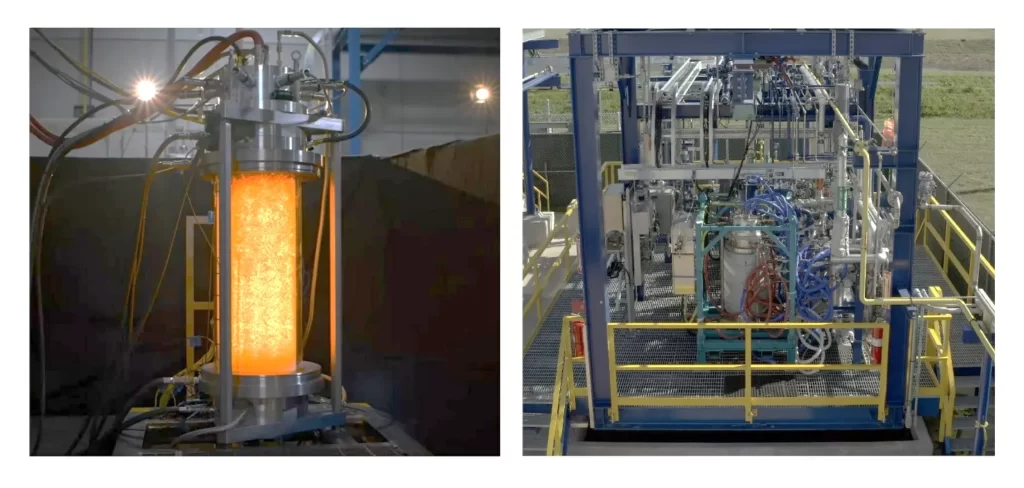
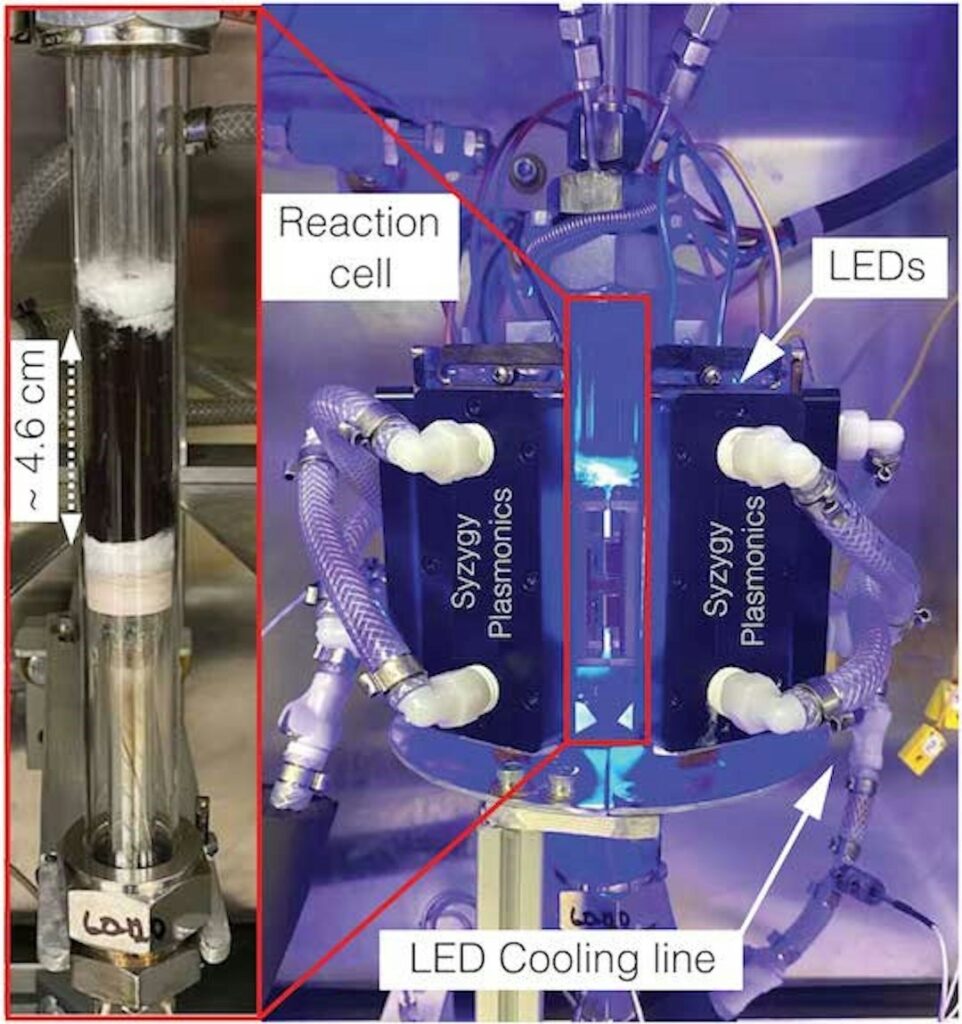
The first experiments were carried out in the small laboratory-scale plant shown in the picture above, but subsequently the company Syzygy Plasmonics, a spin-off of Rice University, assembled a set-up 500 times larger which demonstrated the same efficiency as its lab counterpart for a continuous working time of 1500 hours thus succeeding to extract hydrogen from ammonia at reasonable quantities.
The prototype photo-catalyst unit was called Rigel, is about the size of a washing machine and can produce up to 1 ton/day of H2, a delivery rate which compares favourably with similar devices based on conventional high temperature chemistry.
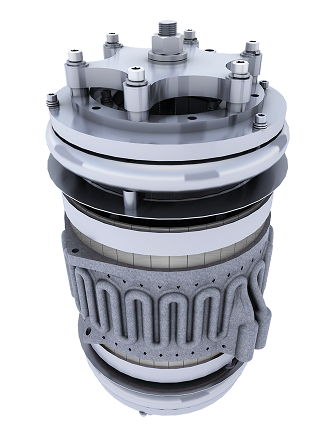
In principle, multiple photocatalyst units may be configured to increase hydrogen production up to a large-scale commercial size.
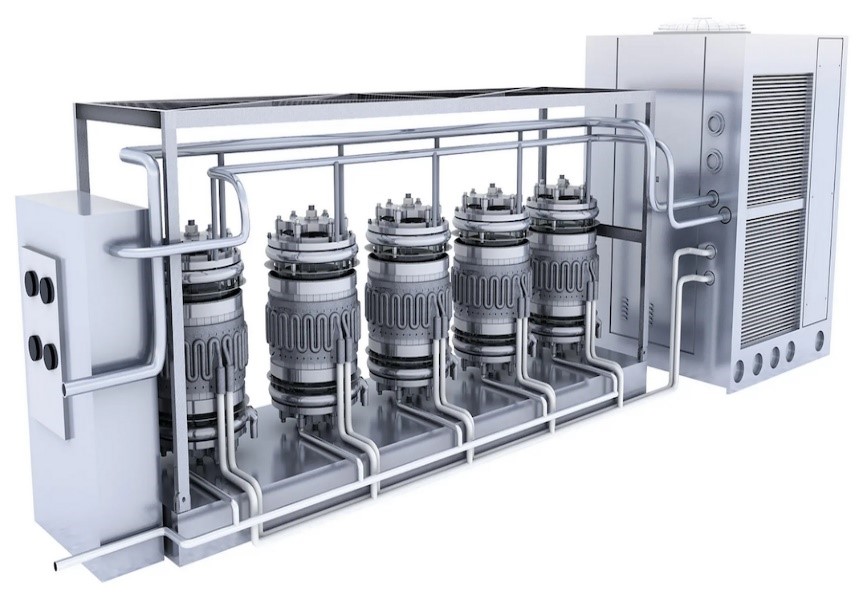
The photocatalytic hydrogen production from ammonia has a great potential for a variety of applications. One important factor is the possibility of building compact devices in relatively contained structures.
Possible future applications of photocatalytic ammonia-to-hydrogen process would be, for example, transporting ammonia on a self-propelled ship as much as it is today done with LNG to deliver it over long distances; or, going further with speculation, one can imagine inserting a small photo-catalyst unit into a car, filling up with ammonia at a service station and then let split-up hydrogen feed the car’s fuel cell.